May 9, 2018
Microwaved plastic increases lithium-sulfur battery life span
WEST LAFAYETTE, Ind. — Purdue engineers have figured out a way to tackle plastic landfills while also improving batteries – by putting ink-free plastic soaked in sulfur-containing solvent into a microwave, and then into batteries as a carbon scaffold.
Lithium-sulfur batteries have been hailed as the next generation of batteries to replace the current lithium ion variety. Lithium-sulfur batteries are cheaper and more energy-dense than lithium ions, which would be important characteristics in everything from electric vehicles to laptops.
But the knock on lithium-sulfur batteries to this point is that they don't last as long, being usable for about 100 charging cycles.
Purdue researchers have found a way to increase the life span in a process that has the added bonus of being a convenient way to recycle plastic. Their process, which was recently published in ACS Applied Materials and Interfaces, shows that putting sulfur-soaked plastic in a microwave, including transparent plastic bags, transforms the material into the ideal substance for increasing the life span of the forthcoming batteries to more than 200 charging-discharging cycles.
“No matter how many times you recycle plastic, that plastic stays on the earth,” said Vilas Pol, associate professor in Purdue’s School of Chemical Engineering. “We’ve been thinking of ways to get rid of it for a long time, and this is a way to at least add value.”
The need to reduce landfills runs parallel to making lithium-sulfur batteries good enough for commercial use.
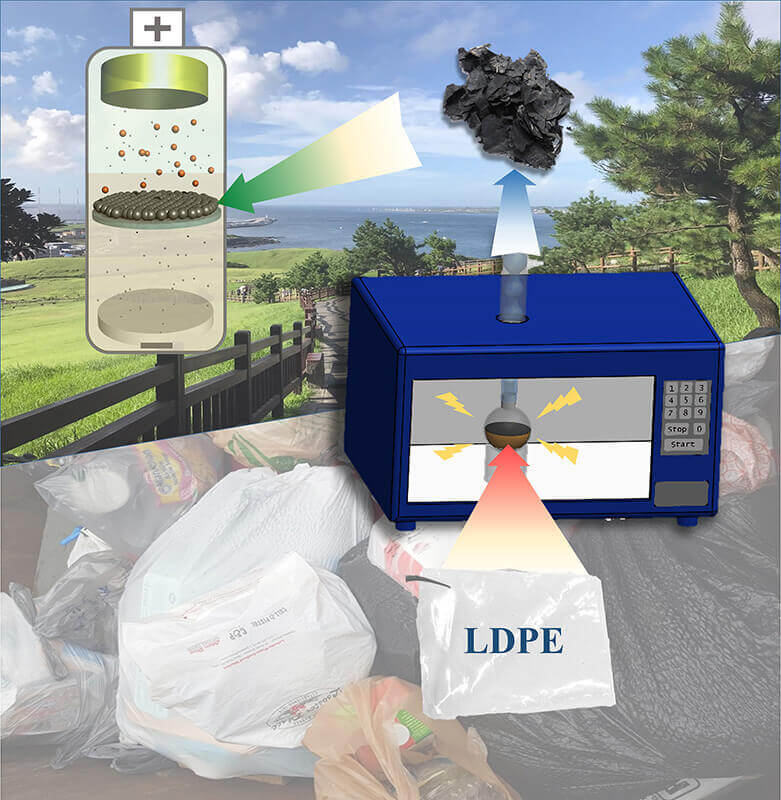
“Because lithium-sulfur batteries are getting more popular, we want to get a longer life sucked out of them,” Pol said.
Low-density polyethylene plastic, which is used for packaging and comprises a big portion of plastic waste, helps address a long-standing issue with lithium-sulfur batteries – a phenomenon called the polysulfide shuttling effect that limits how long a battery can last between charges. Watch a YouTube video explaining this at https://youtu.be/9vgGA4vHaWg.
Lithium-sulfur batteries, as their name suggests, have a lithium and a sulfur. When a current is applied, lithium ions migrate to the sulfur and a chemical reaction takes place to produce lithium sulfide. The byproduct of this reaction, polysulfide, tend to cross back over to the lithium side and prevent the migration of lithium ions to sulfur. This decreases the charge capacity of a battery as well as life span.
“The easiest way to block polysulfide is to place a physical barrier between lithium and sulfur,” said Patrick Kim, a Purdue postdoc research associate in chemical engineering.
Previous studies had attempted making this barrier out of biomass, such as banana peels and pistachio shells, because the pores in biomass-derived carbon had the potential to catch polysulfide.
“Every material has its own benefit, but biomass is good to keep and can be used for other purposes,” Pol said. “Waste plastic is really valueless and burdensome material.”
Instead, researchers thought of how plastic might be incorporated into a carbon scaffold to suppress polysulfide shuttling in a battery. Past research had shown that low-density polyethylene plastic yields carbon when combined with sulfonated groups.
The researchers soaked a plastic bag into sulfur-containing solvent and put it in a microwave to cheaply provide the quick boost in temperature needed for transformation into low-density polyethylene. The heat promoted the sulfonation and carbonization of the plastic and induced a higher density of pores for catching polysulfide. The low-density polyethylene plastic could then be made into a carbon scaffold to divide the lithium and sulfur halves of a battery coin cell.
“The plastic-derived carbon from this process includes a sulfonate group with a negative charge, which is also what polysulfide has,” Kim said. Sulfonated low-density polyethylene made into a carbon scaffold, therefore, suppressed polysulfide by having a similar chemical structure.
“This is the first step for improving the capacity retention of the battery,” Pol said. “The next step is fabricating a bigger-sized battery utilizing this concept.”
This research was funded by the Naval Enterprise Partnership Teaming with Universities for National Excellence Center for Power and Energy Research at Purdue.
Writer: Kayla Wiles, 765-494-2432, wiles5@purdue.edu
Sources: Vilas Pol, 765-494-0044, vpol@purdue.edu
Patrick Kim, kim2698@purdue.edu
Note to Journalists: This paper is available open-access at https://pubs.acs.org/doi/10.1021/acsami.8b03959. A YouTube video is available at https://youtu.be/9vgGA4vHaWg and other multimedia can be found in a Google Drive folder at https://goo.gl/AFQCbZ. The materials were prepared by Erin Easterling, digital producer for the Purdue College of Engineering, 765-496-3388, easterling@purdue.edu.
ABSTRACT
Lithium–sulfur batteries were intensively explored during the last few decades as next-generation batteries owing to their high energy density (2600 Wh kg–1) and effective cost benefit. However, systemic challenges, mainly associated with polysulfide shuttling effect and low Coulombic efficiency, plague the practical utilization of sulfur cathode electrodes in the battery market. To address the aforementioned issues, many approaches have been investigated by tailoring the surface characteristics and porosities of carbon scaffold. In this study, we first present an effective strategy of preparing porous sulfonated carbon (PSC) from low-density polyethylene (LDPE) plastic via microwave-promoted sulfonation. Microwave process not only boosts the sulfonation reaction of LDPE but also induces huge amounts of pores within the sulfonated LDPE plastic. When a PSC layer was utilized as an interlayer in lithium–sulfur batteries, the sulfur cathode delivered an improved capacity of 776 mAh g–1 at 0.5C and an excellent cycle retention of 79% over 200 cycles. These are mainly attributed to two materialistic benefits of PSC: (a) porous structure with high surface area and (b) negatively charged conductive scaffold. These two characteristics not only facilitate the improved electrochemical kinetics but also effectively block the diffusion of polysulfides via Coulomb interaction.
Related websites
“A new polymer raises the bar for lithium-sulfur batteries,” PhysOrg, January 18, 2018
“Lithium-sulfur batteries poised for leap,” Science, March 9, 2018