Purdue’s 3-year mission: High-temperature heat pump technology to cut industrial carbon footprint
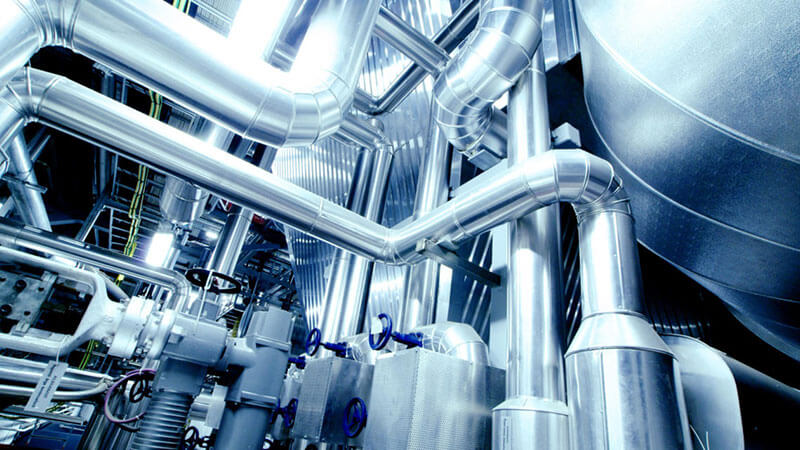
WEST LAFAYETTE, Ind. – The U.S. Department of Energy has made a $3 million investment in Purdue University-led research showing promise to significantly reduce energy use and greenhouse gas emissions in large-scale manufacturing industries.
The planned outcome is novel high-temperature heat pump (HTHP) technology capable of achieving temperatures up to 200 degrees Celsius or 392 degrees Fahrenheit that can be integrated into multiple industrial applications to help decarbonize U.S. industry. HTHP systems harvest low-grade heat using a heat-absorbing refrigerant to compress it and deliver high-temperature heat for use in manufacturing chemicals, pharmaceuticals, paper and food, among other products.
Given immense energy use in manufacturing nationwide, the research could change the game for industry both financially and environmentally. According to the U.S. Energy Information Administration, in 2018, production of chemicals, paper and food accounted for 54%, or 10.5 quadrillion, of the 19.44 quadrillion Btu used by all U.S. manufacturers. A Btu, or British thermal unit, is a measure of the heat content of fuels or energy sources. By comparison, in 2021, all U.S. homes used just 5.04 quadrillion Btu, or about 25% of total industrial use. Cutting electricity usage up to 50% in these large-scale energy-consuming industries would greatly reduce costs and environmental impacts. The DOE’s Industrial Efficiency and Decarbonization Office, which established a roadmap to industrial decarbonization, this summer awarded $135 million in funding for 40 projects that will reduce the industrial carbon footprint toward a net-zero emissions economy by 2050.
Davide Ziviani, Purdue assistant professor of mechanical engineering and associate director of the university’s Center for High Performance Buildings, is leading the three-year, multidisciplinary project involving industrial partners who have a major stake in the mission of decarbonizing the U.S. industrial sector: Trane Technologies, the Shrieve Chemical Co., the Convergent Science engineering software company, GTI Energy and Chemours Co., a chemical research firm. Other collaborators include Oak Ridge National Laboratory and the National Institute of Standards and Technology, which will support advanced manufacturing and working fluid characterizations, respectively.
Ziviani and his team plan to develop a new type of compressor for HTHPs – an internally cooled screw compressor – which operates using two intermeshing helical rotors, known as screws, to compress the refrigerant gas for high-temperature heat delivery.
“The compressor is the heart that makes the system work. Our solution is an integration of the compressor within the system and its cooling that improves efficiency but also has reliability for long-term operation,” Ziviani says.
Creating a new compressor sounds deceptively simple, but there are many complexities to overcome. “Industry is so diverse. You need a technology that is cross-sector and scalable,” Ziviani says. “Each industry has unique processes, so standardizing the production is very, very challenging. You want a technical solution that is flexible enough to be applied to different sectors. The DOE also requires environmentally friendly refrigerants to be employed in HTHPs, adding challenges to identify suitable refrigerants for the target applications that meet flammability and toxicity requirements.”
Another major hurdle is cost. Conventional HTHPs are expensive to install, integrate and maintain, and their efficiency varies. Ziviani says his team will carefully track the operating costs and payback period – the time it takes for their newly developed technology to yield energy savings that recoup industries’ investments in it – to demonstrate to industry the economical efficiency of the technology.
To address these diverse challenges, Ziviani formed a team that includes faculty members, industry stakeholders and national laboratories.
Ziviani says the research will be carried out in three phases. The first year’s work is now focused on initial assessments of the compressor’s design, sizing and fluid selection to establish a framework for the following stages. The second year will involve building the compressor, testing it and optimizing it. “By the end of the second year, we will prove the performance metrics of the compressor itself,” Ziviani says.
In year three, the team will integrate the compressor into the system architecture, test the performance and assess the economics and carbon savings, Ziviani says. “We also have plans for workforce development, which is another critical outcome of the project,” he says. “We will work with our partners to transfer this technology through professional training sessions and seminars. This will go beyond pure research into making a broad impact to the U.S. economy.”
Purdue University collaborating researchers include Riley Barta, assistant professor of mechanical engineering; Rebecca Ciez, assistant professor of mechanical engineering and environmental and ecological engineering; and Eckhard Groll, the William E. and Florence E. Perry Head of Mechanical Engineering and Reilly Professor of Mechanical Engineering. They will support aspects of the research in decarbonization, refrigerants and lubricants as well as system architecture. Ziviani is also working with Purdue’s Institute for a Sustainable Future to promote undergraduate research opportunities and relevant diversity, equity and inclusion activities and outreach covering environmental justice and environmental stressors including air quality, energy efficiency and climate change. Brian Fronk, associate professor of mechanical engineering at Pennsylvania State University, is also a key contributor who will tackle high-temperature heat transfer challenges.
Writer/Media contact: Amy Raley, araley@purdue.edu
Source: Davide Ziviani, dziviani@purdue.edu