Purdue researchers test new materials on International Space Station
When the Space X Falcon 9 rocket launched last weekend to rendezvous with the International Space Station (ISS), it carried special cargo from Purdue: advanced metal and ceramic materials custom designed to test their endurance in outer space.
Outer space presents an environment unlike anywhere on earth. The ISS is exposed to extreme temperature variations and persistent levels of radiation. In addition, it is subjected to a barrage of impacts from micrometeoroids—tiny, irregularly shaped particles that can damage conventional materials.
Xinghang Zhang, Professor of Materials Engineering, and Haiyan Wang, the Basil S. Turner Professor of Materials Engineering, have been developing custom ceramic and metal nanomaterials and testing how they perform under different conditions and environments. Some of these materials can have applications for energy and aerospace, but it is difficult to simulate the environment they will encounter in a nuclear reactor or on a space flight. So, getting to test these materials on the ISS provides a unique opportunity.
“You just don’t have that kind of testing capability on Earth,” Zhang said. “We get a chance to take materials fabricated here and test them in outer space under extreme environment.”
The team will be studying the radiation resistance of stainless steel and a nickel alloy produced by additive manufacturing, widely used in academia and industry. They will also be testing the impact resistance of nanostructured ceramics made from titanium dioxide against micrometeoroids. The project is part of NASA’s Materials International Space Station Experiment (MISSE), a series of missions where material samples are mounted on the outside of the ISS to test their performance.
Space on the ISS is precious. The Purdue team has about a square inch to place their material samples inside a tray mounted on an arm outside the station. Ben Stegman and Bo Yang, graduate students in Zhang’s lab, 3D printed special containers in Purdue’s Flex Lab with a grid of slots that can hold the samples. The container is also fabricated from one of the test metals and will act as a sample itself.
Bo Yang also developed the titanium dioxide ceramics with a special process called flash sintering. Normally the process to produce such ceramics takes very high temperatures over several hours, but flash sintering applies an electrical field to speed up the process within minutes at much lower temperatures. It also produces a much finer grain size that could have better plasticity to withstand impacts.
The CRS-23 Dragon spacecraft docked safely to the ISS on Aug. 30. Once the samples are launched and mounted on the ISS later this fall, they will spend six months exposed to the space environments. When they are returned, the team will analyze the microstructures of both the metallic alloys and ceramics to see how they responded to the extreme conditions and changed over time, looking for changes in grain sizes or for cracks and deformations in the materials.
Zhang says he is excited about the opportunity to test these materials in outer space, and hopes that this Purdue-ISS collaborative will attract talented students to apply to Purdue’s grad school for materials research.
“As a material scientist, we’ve been studying radiation tolerance properties in materials for two decades, and we have never had an opportunity to send samples to outer space. So, that itself is a precious opportunity,” he said. “We keep developing new materials on Earth by using different chemistry and fabrication techniques that we believe has a better performance, but we never know if or how they survive in outer space. Now we can test some outstanding materials that may survive in extreme environments, which is exciting because then that can promote us to design better materials for outer space exploration.”
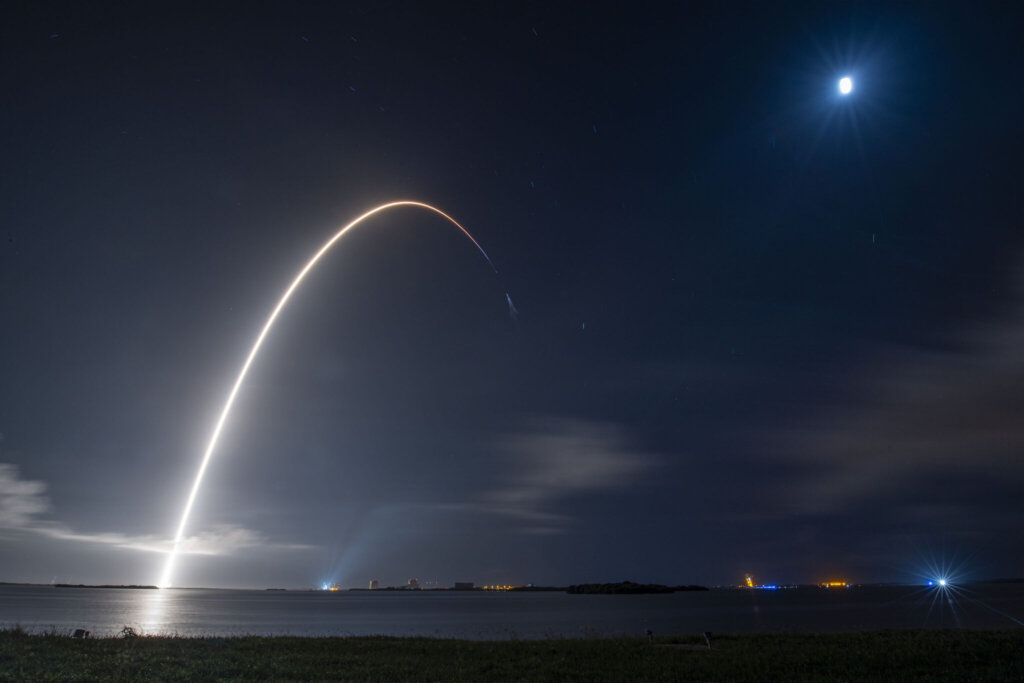