Morphing aircraft systems developed by Purdue researchers aim to enhance performance of hypersonic vehicles
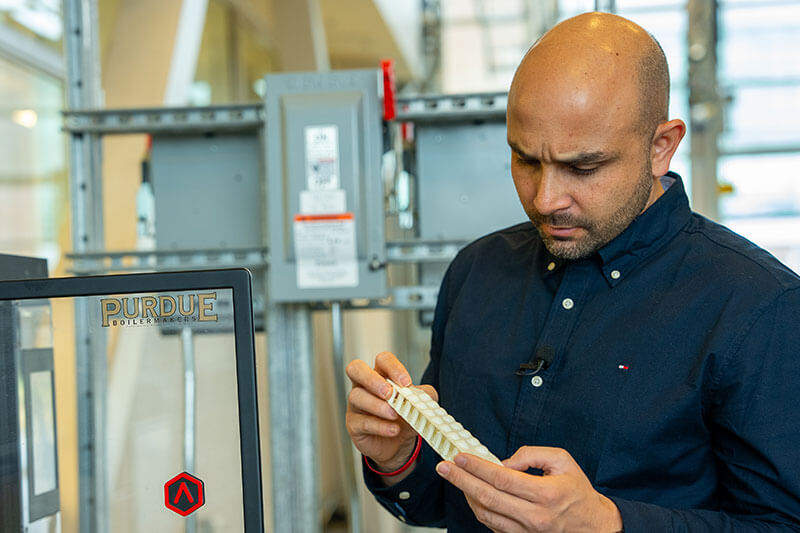
WEST LAFAYETTE, Ind. — What if components in aircraft could morph in response to their external conditions, much like a bird changes the shape of its wings? And what if those components could function like an octopus arm, operating independently of a central control system? Inspired by these natural phenomena, a Purdue research team is developing morphing systems for hypersonic vehicles that respond to their environment.
Current hypersonic vehicle designs are highly efficient, but only in specific, preset conditions. As aircraft exceed speeds of Mach 5, the external conditions acting on the body of the vehicle change dramatically. For example, a vehicle designed to perform at Mach 5 conditions becomes increasingly inefficient as it climbs to speeds of Mach 10.
To combat this problem, Andres Arrieta, associate professor of mechanical engineering, and Rodney Trice, professor of materials engineering, are designing aircraft systems with multistable structures — components that can take on multiple shapes in response to external forces. These structures function through a combination of mechanical and material interventions that not only make morphing hypersonic systems possible but may also reduce weight and complexity.
“Current mechanisms that help aircraft maneuver, like the aileron or tail, create noise and drag,” Arrieta said. “These mechanisms are also chains of different parts, and each of these parts are joined by a joint. The more parts and joints you have, the more complex your system becomes. So if we have a structure that is just one big part but is also capable of deforming, then there is potential to reduce not only complexity but also failure, maintenance costs and weight — which is the most important consideration in aviation.”
Developing this type of system requires advanced sensing technology localized to and controlled within the morphing components. The inherent structural responsiveness is programmed to reshape the component depending on conditions such as temperature and speed. This technology is completely independent from other devices that typically control an aircraft’s movement, such as microprocessors and actuators.
“Think about something like an octopus arm that can perform certain behaviors in a completely autonomous way without having to tap into the brain,” Arrieta said. “Similarly, you can create a software program embedded into the structure that is locally processing information and morphing without any input from a central processor.”
The goal is to create a surface that can take on a variety of shapes so the aircraft can maintain optimality over a range of speeds, temperatures and altitudes.
Typically, hypersonic vehicles are designed using a material, like ceramic, that is strong enough to withstand the immense heat and pressure generated at high speeds. However, ceramics have a low strain-to-failure rate, which means they easily break during the process of deformation.
Trice, who specializes in high temperature ceramics and ceramic processing, is developing a new type of ceramic surface that can morph without straining and is capable of withstanding temperatures above 1,300 degrees Celsius. These ceramic components will then be fabricated using an additive manufacturing process that Trice and his graduate students have matured.
“It is the recent advances in additive manufacturing that enable fabrication of the complex ceramic parts that can bring Professor Arrieta’s designs to fruition,” Trice said. “We are incredibly excited to be working on this idea in collaboration with him.”
The development of this process is supported by a grant from the Air Force Research Laboratory (AFRL) Regional Network — Midwest, a new science and technology ecosystem that connects AFRL scientists and engineers with researchers from universities, businesses, government agencies and venture capitalists. Arrieta and Trice’s research team is collaborating with two AFRL scientists as well as Canopy Aerospace and Stratolaunch LLC with the goal of transitioning their technology to the defense and industry markets.
“The project is an innovative fusion of material science and mechanical design. It’s great to see the Midwest Regional Network forge these types of public-private partnerships to address pressing DOD (Department of Defense) challenges,” said Phil Buskohl, a materials research scientist in the Functional Materials Division at AFRL. Buskohl and research engineer Nathan Hertlein are the AFRL technical sponsors for this project.
This work is also funded through a National Science Foundation Faculty Early Career Development (CAREER) Program Award, which has supported the development of the basic mechanics associated with these structures. Additionally, the Defense Advanced Research Projects Agency’s Nature as Computer program provided funding to develop embedded computing and sensing concepts.
About Purdue University
Purdue University is a public research institution demonstrating excellence at scale. Ranked among top 10 public universities and with two colleges in the top four in the United States, Purdue discovers and disseminates knowledge with a quality and at a scale second to none. More than 105,000 students study at Purdue across modalities and locations, including nearly 50,000 in person on the West Lafayette campus. Committed to affordability and accessibility, Purdue’s main campus has frozen tuition 13 years in a row. See how Purdue never stops in the persistent pursuit of the next giant leap — including its first comprehensive urban campus in Indianapolis, the new Mitchell E. Daniels, Jr. School of Business, and Purdue Computes — at https://www.purdue.edu/president/strategic-initiatives.
Writers: Lindsey Macdonald, macdonl@purdue.edu
Bryan Ripple, Air Force Research Laboratory Public Affairs Office, bryan.ripple@us.af.mil
Sources: Andres Arrieta, aarrieta@purdue.edu
Rodney Trice, rtrice@purdue.edu
Phil Buskohl, Air Force Regional Laboratory